For today’s CPGs, particularly those packaging food and dairy products, understanding the correct process for qualifying new products and packaging materials is essential. To compete in today’s marketplace, your brand must be packaged sustainably, cost-efficiently and it must have differentiated shelf appeal in the supermarket. Each of these factors will pressure you to make changes to your packaged product offering, but how can you do so quickly, affordably and with minimal risk?
In this blog post, we will guide you through the optimal process for qualifying new products and packaging on your existing machinery. We will highlight the significant benefits of following this process and shed light on the risks of not doing so. We will also share examples of specific products and services that Synerlink offers to help customers navigate their particular qualification journey.
How to Care for Your Equipment, the guide This is the fifth chapter of a full guide to help you on your packaging equipment maintenance. Subscribe below to receive the complete guide as soon as it is released! .png?sfvrsn=9f354794_3)
| 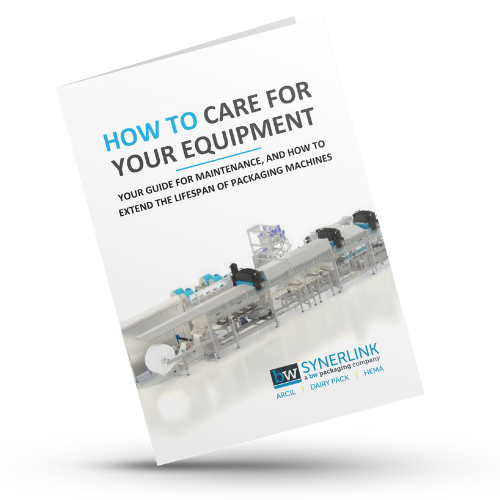
|
THE RISKS & REWARDS OF MATERIAL AND PRODUCT QUALIFICATION
Brand owners may need to qualify new products and materials for various reasons, with sustainability being a prominent driver in today's market. From sourcing packaging materials to enhancing shelf appeal and increasing market share, the motivations for changing a packaged product are diverse.
However, attempting to qualify new products or materials without the assistance of your OEM poses significant risks. Brand owners who go it alone are likely to encounter unforeseen issues during production such as machine breakdowns, damaged product or losses in production capacity. Any of these issues can leave you unable to package and deliver your products to customers. The implications of this can include additional costs, production delays, and even the loss of customers.
By involving your OEM from the start, you can establish a clear path to production with the new product or package. Real test results allow for incremental decision-making, minimizing the risk of an unsuccessful launch. Working closely with your OEM throughout this process provides valuable insights, including a practical timeline for product launch, accurate cost estimations, and a well-defined plan of action after qualification.
HOW TO QUALIFY NEW PACKAGING MATERIALS AND PRODUCTS
To navigate product and material qualification successfully, Synerlink recommends a three-step qualification process. This rigorous approach ensures that new packaging materials and products meet the necessary standards and are seamlessly integrated into the CPG’s production line.
1) Lab Tests
The first step in qualifying a new packaging material or product is lab testing. During lab testing, Synerlink’s experts analyze the new material or product at a dedicated Synerlink facility and compare it against existing products and materials within our database. The primary purpose of the lab test is to identify potential risks that may arise during the subsequent stages of the qualification process.
These lab tests are tailored to the unique requirements of each project. For instance, when qualifying a new preformed cup, we may want to test the sealing process to ensure food safety standards are properly addressed. For form-fill-seal (FFS) applications, tests may be more complex and involve examining how the material holds up when multiple cups are stacked in cartons or pallets. For example, Synerlink can simulate the weight that would bear down on plastic cups near the bottom layers of a pallet when multiple (15-20) layers of cups are stacked in your production plant. By applying similar levels of pressure to cups in the lab, you can ensure your actual production process results in cups that are in perfect shape when they arrive to the retailer. For PET multipacks, you’ll likely want to test the cutting and pre-cutting of this material on a solution such as Synerlink’s Snapcut technology.
Whatever the case may be, lab testing is a critical step in the qualification process because it helps identify potential risks that can be evaluated further during on-site testing.
2) On-Site Tests
The second step in the qualification process is the on-site test. This phase aims to simulate how the new material or product will perform in your real-world production and packaging environment. Thanks to the insights gained previously during lab testing, you can enter this stage with crucial information about the machine adjustments required to ensure successful integration. On-site testing serves as an opportunity to fine-tune the final solution. It validates ideas and observations made during the lab tests.
However, it can also reveal major issues that weren’t identified in the lab, which is advantageous as it allows you to address these problems before full-scale production begins. It’s not possible to replicate every production constraint perfectly in a lab. For example, suppose you’ve selected a new sustainable material (e.g., PET) for your FFS yogurt production line. Lab tests may have initially indicated that everything is in order, so you feel comfortable bringing the material into production. However, challenges occur when you change over from the old PS material to your new PET material. It seems during extended downtime, the material has cooled back down, resulting in alterations and irregularities in the packaging, therefore resulting in ample product waste.
On-site testing allows you to identify and address these real-world risks before you bring a new packaged product to market.
3) Tests Report & Action Plan
Following the completion of lab tests and on-site tests, Synerlink provides a comprehensive test report to their customers. This report serves as a common analysis of the viability of the new product or packaging material. It includes a detailed explanation of the test results, highlighting all the risks and issues identified during testing.
Crucially, the test report also offers an action plan for addressing any challenges discovered during testing. This plan may involve machine overhauls, upgrades, or even collaboration with the supplier of the new packaging materials to make necessary adjustments. Ultimately, the test report is an invaluable resource that empowers CPG companies with a clear understanding of the timing, cost, and potential risks associated with bringing a new product to market.
COMMON OUTCOMES OF A QUALIFICATION ACTION PLAN
Thanks to Synerlink’s deep knowledge of packaging materials and machinery, our customers have a distinct advantage when navigating the qualification process. We’ve already encountered and resolved many of the challenges our customers are likely to face, and therefore, we can proactively recommend proven solutions for common customer challenges. Below are some of the common actions we recommend to customers to help them execute a successful, predictable launch.
Upgrading the Machine
Switching from PS to PET or PP will require heavy changes on your machine if it was not designed for it. Changes from one material to another, for example, can change the heating and cooling requirements of the machine to ensure perfect cuts, among other considerations.
Overhauling the Machine
Depending on the cup you are running on an FS machine, some areas can be more or less sensitive regarding adjustment and weariness. If you are introducing a more difficult cup, overhauling some modules of the machine might be necessary but sufficient to keep a high machine efficiency.
Request Change to Materials
Switching from an HDPE bottle to a PET bottle can create an issue at bottle introductions. The hardness of PET makes it more difficult to insert the bottles into the plates. A potential solution is very slightly reducing the neck diameter of the new PET bottle. Synerlink can facilitate all required material change requests on behalf of our customers.
Upgrade or Change The Dosing Unit
Increasing the size of fruit pieces will require nozzles to have a big enough opening to let the fruit pieces through. In this scenario, Synerlink might change the nozzle entirely.
Did you find this content useful? Click the link below to download our comprehensive guide to getting the most value out of your existing Synerlink equipment.
How to Care for Equipment: Top 5 Ways to Extend the Life of Your Packaging Machinery